Logistics Center
EDEKA
A logistics project
of superlatives
To manage a mega-project like this, it was divided into three construction phases. The construction began with Phase No. 3, which is also the tallest. The parapet height here ranges from 27 to 36 meters. Given the clear disadvantages of heavyweight concrete components in terms of transportation and installation at this height, it was essential to incorporate as much lightweight material as possible, such as material-efficient load-bearing elements made of glued laminated timber. Consequently, auxiliary and support beams, as well as most central and perimeter columns, were planned and executed in glued laminated timber. Due to the relatively high snow load of approximately 220 kg/m², the cross-sectional dimensions were comparatively large.
However, the most significant challenge lay in the three-dimensional bracing of the very tall building complex. A large glued laminated timber truss system was used to form a roof slab, redirecting wind loads to the massive wall slabs. Cantilevered strut supports at this height are too flexible and would not have been able to achieve this in a material-efficient manner. A special feature is the hybrid supports at the edge of the building: these are - half precast concrete, half wooden support - rigidly connected, thus combining the strength of each material.
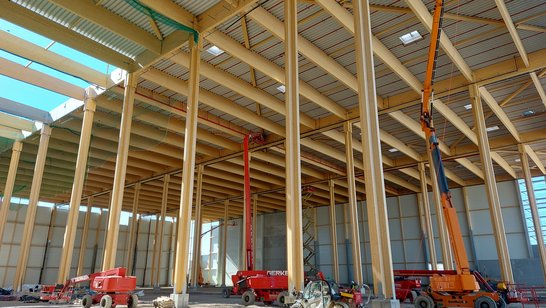
Thoughtful
Concept
To solve the challenges, a high level of coordination with the on-site planners and inspectors was necessary to ensure both the vertical and, especially, horizontal load flow from the roof to the foundation.
During the installation, a thoughtful concept was required, which the experienced assembly team at WIEHAG executed. Temporary bracing of the 36m high columns and favorable weather conditions were particularly crucial.
For the lower construction phases No. 1 and 2 with a parapet height of approximately 14 meters, the main task was to produce the large-volume beams quickly and deliver them just-in-time to the construction site. WIEHAG ensured this through an efficient process from planning, production, to logistics, all under one roof. Swift installation of the bracing struts was secured by the in-house WIEHAG standard connections with a pure steel-to-steel connection. The largest glued laminated timber beams, with a cross-section of 32/330cm, were block-glued in width and height, weighing approximately 17 tons.
The construction of the new Edeka logistics site aimed to be as energy-efficient as possible. With a large-scale photovoltaic system and combined heat and power units, a portion of the required electricity is self-produced. Additionally, the more than 40,000 m² of roof area is greened.
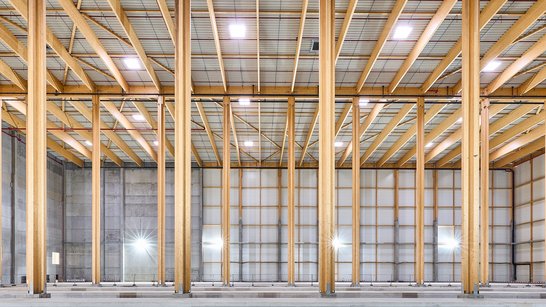
- Client
- EDEKA Nordbayern Bau- und Objektgesellschaft mbH
- Planner/Architect
- pbb Planung + Projektsteuerung GmbH
- Location
- Marktredwitz, Germany
- Scope of Work
- Statics & Construction, Work Planning, Production, Transport Logistics, and Installation
- Glued Laminated Timber Volume
- 13,200 m³
- Hall Area
- 95,000 m²
- Wood Construction Period
- September 2022 – July 2023
- Weight of Steel Connectors
- Total 125 tons
- Logistics
- Over 250 truck transports